Feature
How is a truck made?
It is difficult to ignore the simple, pure majesty of the truck. Towering above the majority of popular vehicles, the construction of the truck is an engineering feat in itself, paving the way for new industries and easing the logistical and time-consuming nightmare of small-vehicle transport. In the following article, we will strip back the truck in its entirety to understand the process in which our beasts of the road come to be.
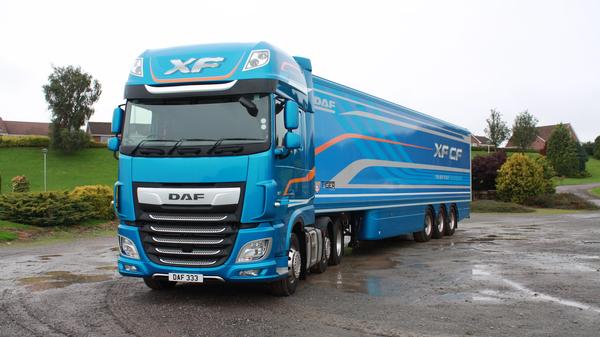

Words by: Auto Trader
Published on 2 December 2020 | 0 min read
What materials is a truck made of?
Generally, steel has always been the popular choice for truck engineers, famed for its durability and consistent strength. Aluminium is required for its incredibly lightweight, but also crucial for its corrosion-resistant qualities, allowing trucks to reach the levels of long-term durability required by their drivers. Finally, the trademark truck shape relies on cutting-edge moulded plastics.
The cab structure and outer layer again favour the popular choice of steel or aluminium; however, if steel is chosen then extra practices are taken to protect it from corrosion - zinc is one popular barrier. The famous fenders often require the malleable properties of plastic or fibreglass to guarantee the aerodynamic angles. The exterior trim of the truck including mirrors and grab handles favour the stylishness of polished stainless steel, adding an aesthetically fine touch and ensuring no cracks or weather damage.
The cab structure and outer layer again favour the popular choice of steel or aluminium; however, if steel is chosen then extra practices are taken to protect it from corrosion - zinc is one popular barrier. The famous fenders often require the malleable properties of plastic or fibreglass to guarantee the aerodynamic angles. The exterior trim of the truck including mirrors and grab handles favour the stylishness of polished stainless steel, adding an aesthetically fine touch and ensuring no cracks or weather damage.
And the interior?
Truck drivers often spend extended periods of time behind the wheel, hence the manufacturing attention continues behind the driver doors. The interior of the cab normally uses either vinyl or cloth upholstery, with the floors normally carpeted or using rubber mats. Moulded plastic is again used for the common dashboard and laminated safety glass for the windows.
The process of building a truck
The truck industry has come a long way since the first designs of the late 19th century; however, the original essence remains and lives on in the new designs of trucks that emerge every 5-6 years.
For the most part, truck manufacturers tend to build their own cabs, some even building engines and axles etc. However, due to ever-increasing demand and logistical ease, some major components are out-sourced and shipped to the assembly plant. Some assembly plants are fascinating places, with groups of workers adding successive components as the vehicle creeps down the line. Starting as a frame skeleton and ending as a completely functioning truck, even being driven off the end of the assembly line.
For the most part, truck manufacturers tend to build their own cabs, some even building engines and axles etc. However, due to ever-increasing demand and logistical ease, some major components are out-sourced and shipped to the assembly plant. Some assembly plants are fascinating places, with groups of workers adding successive components as the vehicle creeps down the line. Starting as a frame skeleton and ending as a completely functioning truck, even being driven off the end of the assembly line.
The production line
Initially, large presses crunch steel into the various required shapes needed for specific components, these are then temporarily left to one side.
For the frame, long steel rails are carefully fed through a machine, which then drills up to 200 holes per beam (depending on the requirement of the model) for bolts and lines, after they have all been sliced to the right length, normally using a state-of-the-art laser cutter. As the chassis drifts slowly down the production line ready for its next attachment, workers diligently attach other important members, sub-frames and the engine mounts. Many trucks up to this point will be upside down, allowing the sizeable, weighty axles to be dropped on to the chassis a lot more easily, often using an overhead crane! Following the basic assembly, the chassis is sent onto its next stage where it will be spray painted before any additional processes. This is no easy job, workers often wear bio-suits and rely on built-in oxygen lines to be able to do their job properly, and safely! Electrical lines and air hoses follow in the next stages, then followed by the wheels (still fitted upside down) before the chassis is finally flipped over to allow for the final placement of the engine and transmission. This is not the only activity going on here. On the other side of the factory, workers assemble and paint the cabs. Most manufactures use a very clever method of priming the cabs- after dipping in a special primer, an electrical current is run through the liquid, and in doing so attracts the paint to all hard to reach areas of the cab. The cabs generally receive two coats, with an intermittent 140 degrees bake and a light buff to eradicate impurities. Finally, using UV technology to illuminate imperfections the truck goes through its final pre-road procedures, and after its final lowering onto the chassis, the truck as we know it is finally born. Following a short testing period including a small road test, the truck is finally ready for its maiden voyage. The extensive care, production quality and intensive procedures involved in the production of the truck are crucial in maintaining its reputation of long-standing durability.
For the frame, long steel rails are carefully fed through a machine, which then drills up to 200 holes per beam (depending on the requirement of the model) for bolts and lines, after they have all been sliced to the right length, normally using a state-of-the-art laser cutter. As the chassis drifts slowly down the production line ready for its next attachment, workers diligently attach other important members, sub-frames and the engine mounts. Many trucks up to this point will be upside down, allowing the sizeable, weighty axles to be dropped on to the chassis a lot more easily, often using an overhead crane! Following the basic assembly, the chassis is sent onto its next stage where it will be spray painted before any additional processes. This is no easy job, workers often wear bio-suits and rely on built-in oxygen lines to be able to do their job properly, and safely! Electrical lines and air hoses follow in the next stages, then followed by the wheels (still fitted upside down) before the chassis is finally flipped over to allow for the final placement of the engine and transmission. This is not the only activity going on here. On the other side of the factory, workers assemble and paint the cabs. Most manufactures use a very clever method of priming the cabs- after dipping in a special primer, an electrical current is run through the liquid, and in doing so attracts the paint to all hard to reach areas of the cab. The cabs generally receive two coats, with an intermittent 140 degrees bake and a light buff to eradicate impurities. Finally, using UV technology to illuminate imperfections the truck goes through its final pre-road procedures, and after its final lowering onto the chassis, the truck as we know it is finally born. Following a short testing period including a small road test, the truck is finally ready for its maiden voyage. The extensive care, production quality and intensive procedures involved in the production of the truck are crucial in maintaining its reputation of long-standing durability.